Calibration service suppliers can check your instruments in their facilities, or they can send a field technician out to you upon request. Some suppliers, such as Fluke Calibration and Fluke Calibration’s other brands, will allow you to rent test equipment.
Calibration servicers calibrate instruments and tools based on standardized measurements established by metrology. Using their instruments, technicians will measure and calibrate your instruments per your needs, such as unit of measurement type and required measurement accuracy per standards and regulations.
The procedure that technicians follow during the calibration process can be summed up by the following three step descriptions: 1) definition of unit to be measured, 2) realization of measurement, and 3) traceability to a quantitative rating.
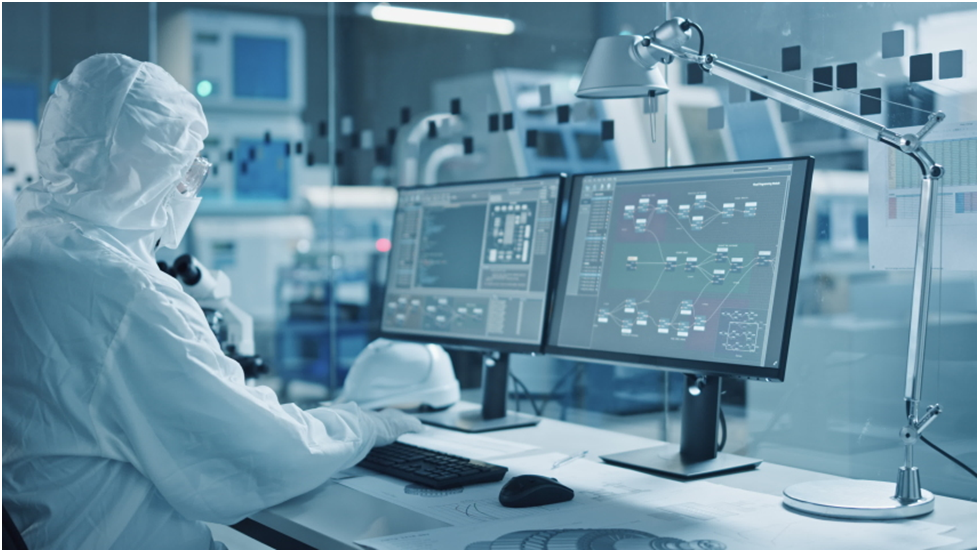
1. Definition of Unit to be Measured
Examples of units that technicians often define and measure include units of distance (anywhere from micrometers to light years), volume, mass, time, strength, flow, longitude, distance and temperature.
2. Realization of Measurement
Once technicians define the unit of measurement, they transfer them to a quantifiable scale, where they create ratings. They then measure the tool or instruments level of output or allowance of this unit.
3. Traceability to a Quantitative Rating
After measuring, technicians apply a rating to the results. They then compare it to a baseline and record their results. By recording their results, they create traceability.
Once technicians have taken these steps, they can finally adjust the measured instrument until it matches the accepted measurement or reads accurately.
Something that calibration service providers also do is occasionally calibrate and test their own test equipment. They do so on a schedule that they call the calibration interval. By doing so, they maintain their integrity and the quality of their services.
Machinery Used
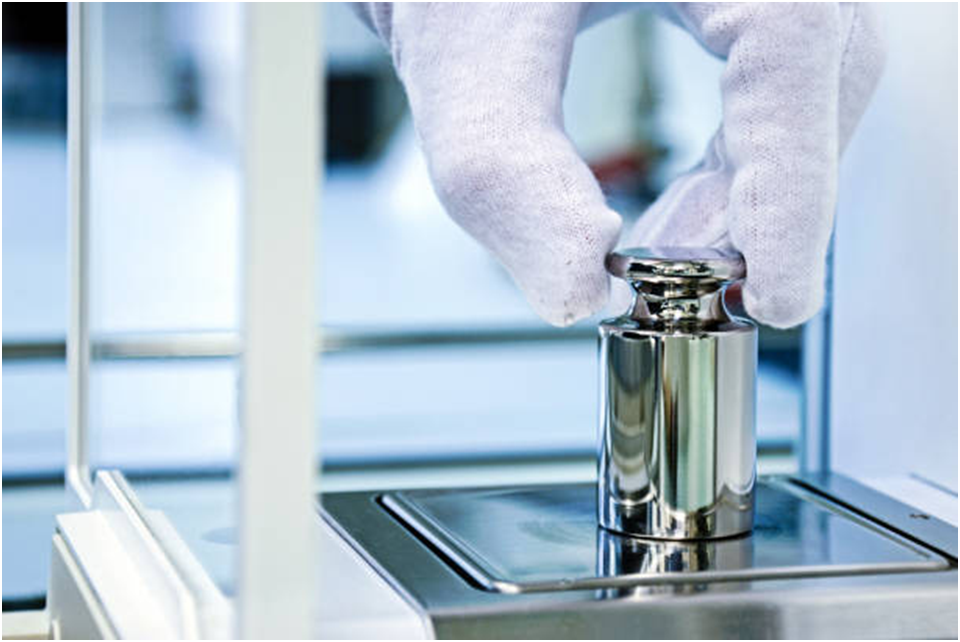
To carry out the many different types of calibration out there, calibration service providers use a wide variety of calibration tools and machines. These include those that are handheld, fixed, and portable.
Handheld calibration devices are usually small and manually operated.
Fixed calibration instruments remain stationary. They are used in factories and other workplaces during production as needed.
Portable devices may be large and mounted on wheels so that they can be moved around a facility as needed.
Variations and Similar Processes
Traceable calibration is a type of calibration that involves comparing established traceable standards to a series of an instrument’s measurements. Traceable calibration allows technicians to most accurately account for an instrument’s quirks, such as precision and bias. It also helps them pick up on fluke readings.
Pipette calibration is used in medical and laboratory settings. A pipette dispenses measured quantities of liquids for lab or medical use. Accuracy is critical in these environments, so the pipette must be calibrated correctly.
Torque wrench calibration is commonly used on the nuts and bolts of more basic applications. Torque, the product of force and distance, can be calibrated on a torque wrench for improved accuracy. This is important for the threading of nuts and bolts so that over or under-tightening does not occur.
Load cell calibration helps to yield accurate weight measurements in scales. Load cell calibrators are often handheld. To use them, technicians plug them into a transducer with a ready load cell. The calibrator, which has been pre-standardized, takes a weight measurement of that which the load cell is also measuring. The results read out on the device, separate from the results on the load cell. Technicians then adjust the load cell until the calibrator and transducer produce the same reading.
Scale calibration is the process of calibrating weighing scales, such as laboratory scales or industrial scales. Often, this involves load cell calibration, since so many scales use load cells.
Multimeter calibration is the calibration of multimeter equipment. Multimeters are devices that measure electric voltage, current, and (usually) resistance.
Hardness tests measure the hardness of a given material. Hardness tests provide valuable information like the level of resistance to deformation.
Calibration laboratories are laboratories where professionals provide testing to smaller equipment and instruments. Calibration labs often work in conjunction with on-site calibration services. One of the most common tools that technicians use in a calibration laboratory is the pipette.
Pressure calibration is a calibration service that operators perform on instruments that measure control or pressure.
Temperature calibration is specifically for devices that measure or control temperatures, like detectors or thermostats.
Speedometer calibration is a service that helps a speedometer accurately measure speed in a vehicle or some other piece of machinery. It keeps the reading precise and properly accounting for distance. In automotive applications, this precision keeps drivers safe by giving them the information that they need to drive within the speed limit.